Oatly Manufacturing is a fully automated, sealed system. The only human contact is at the connection point between the rail car full of oats, the raw product of Oat Milk, and the pump.
The process of turning raw oats into their products —including milk and ice cream— begins with making a paste by adding water to the oats, which is then pushed through the entire system. This slurry is added to giant pressure cookers along with flavoring and processed into their base products.
A hallway divides processing from packaging. The packaging process packs base products into containers that are palletized autonomously, picked-up with a forklift, and loaded onto a truck.
The staircases and alternating tread ladders were suspended from the roof of the building to create a seven-foot-tall mezzanine level for service. This elevated, IMP walkable control room above the processing and packaging floor contains a computer monitoring system and allows eyes on the system.
FFKR’s scope of work included coordination of the mechanical and electrical and large footings for the owner-provided equipment. Special accommodation was taken to have pipe racks sixteen feet above the manufacturing floor allowing forklift travel below.
Oatly Manufacturing was a renovation of an existing building. To accommodate the equipment, the interior of the building was completely demolished except for the tilt-up walls and the most of the concrete slab-on-grade. IMP panels were used for ceilings and walls within the clean area space and were used to delineate smaller interior spaces. IMP panels were selected because they are easy to clean and erect on a tight schedule because it does not require sanding or painting.
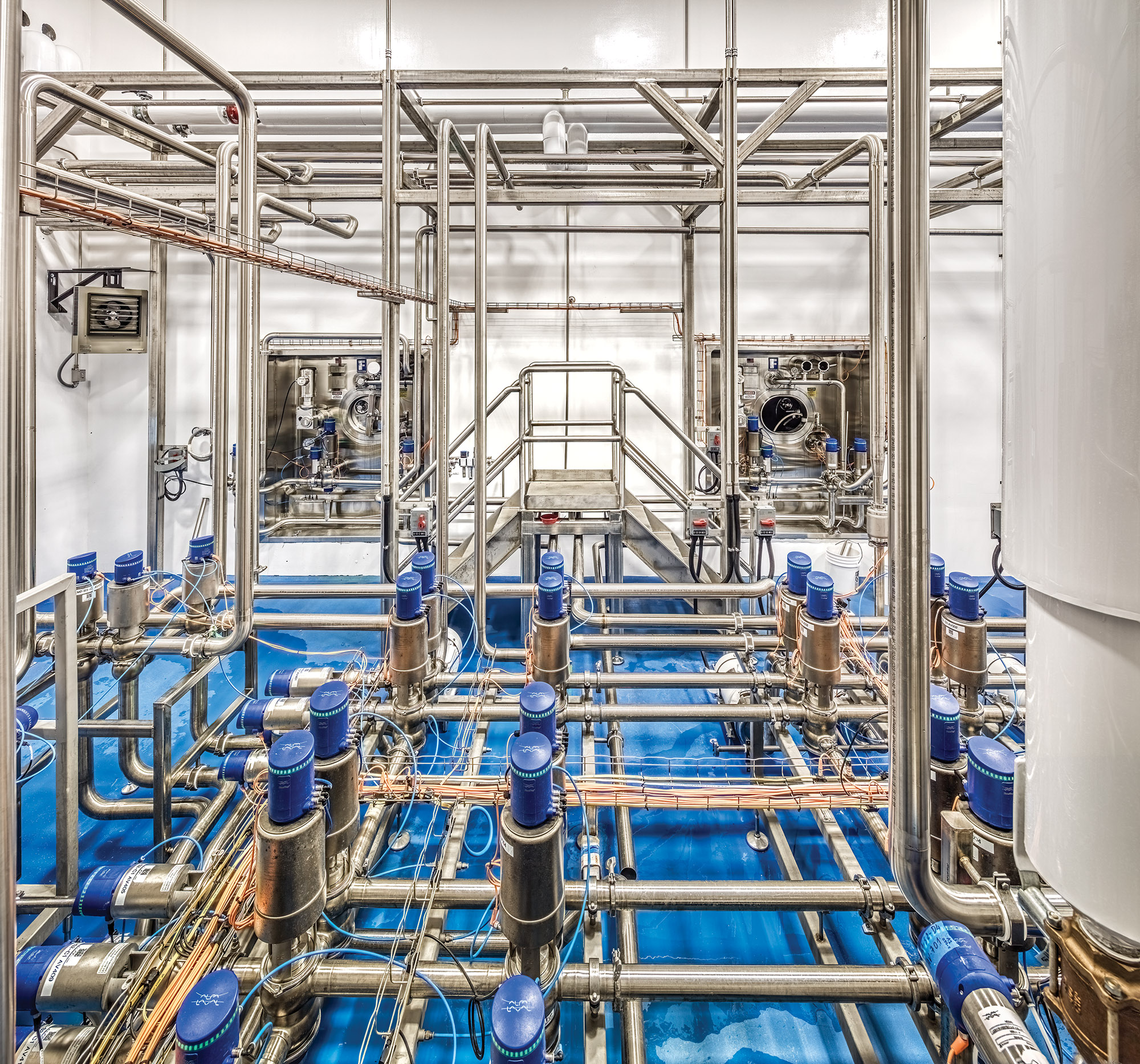
Title
Caption
Title
Caption
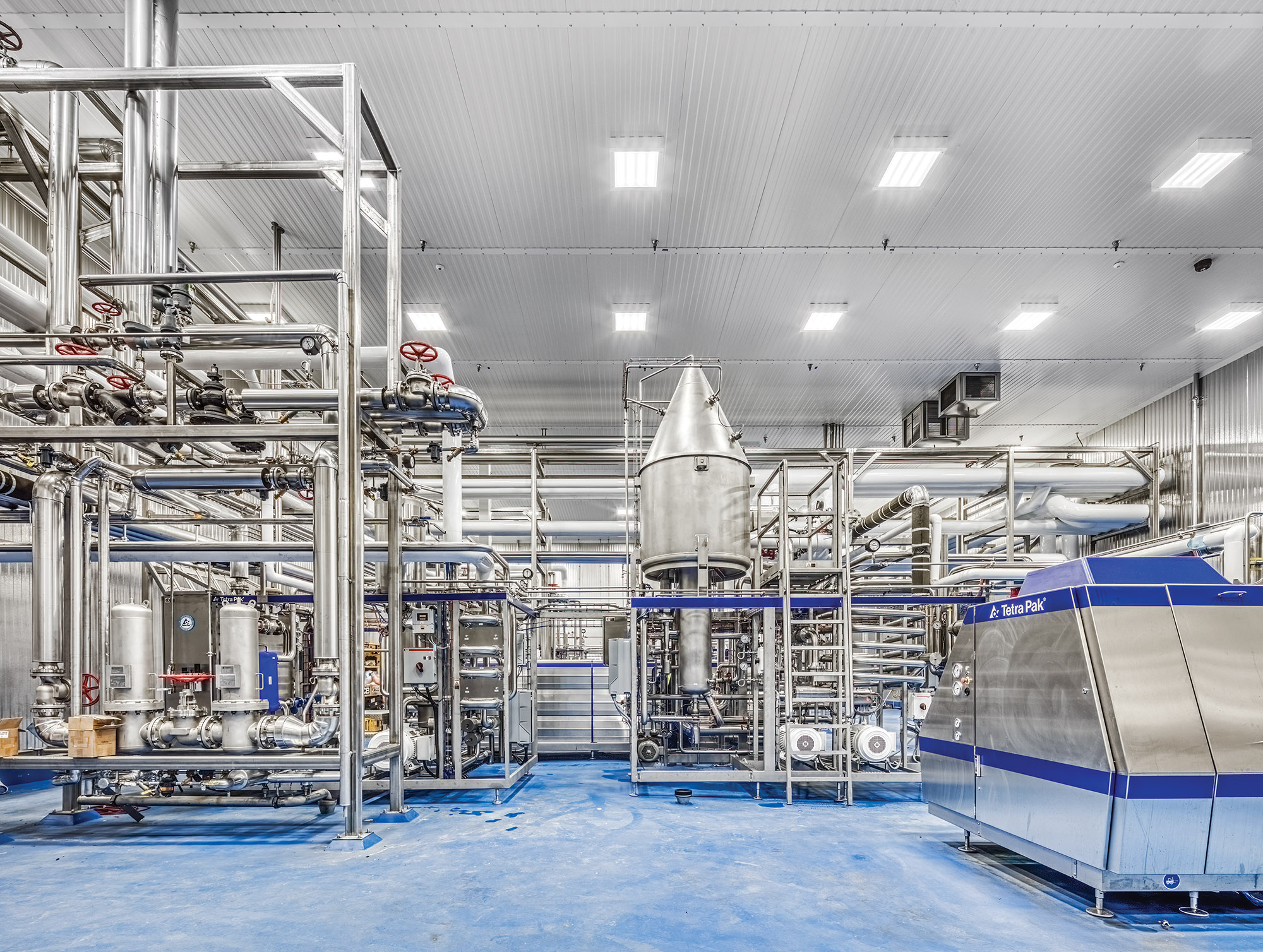
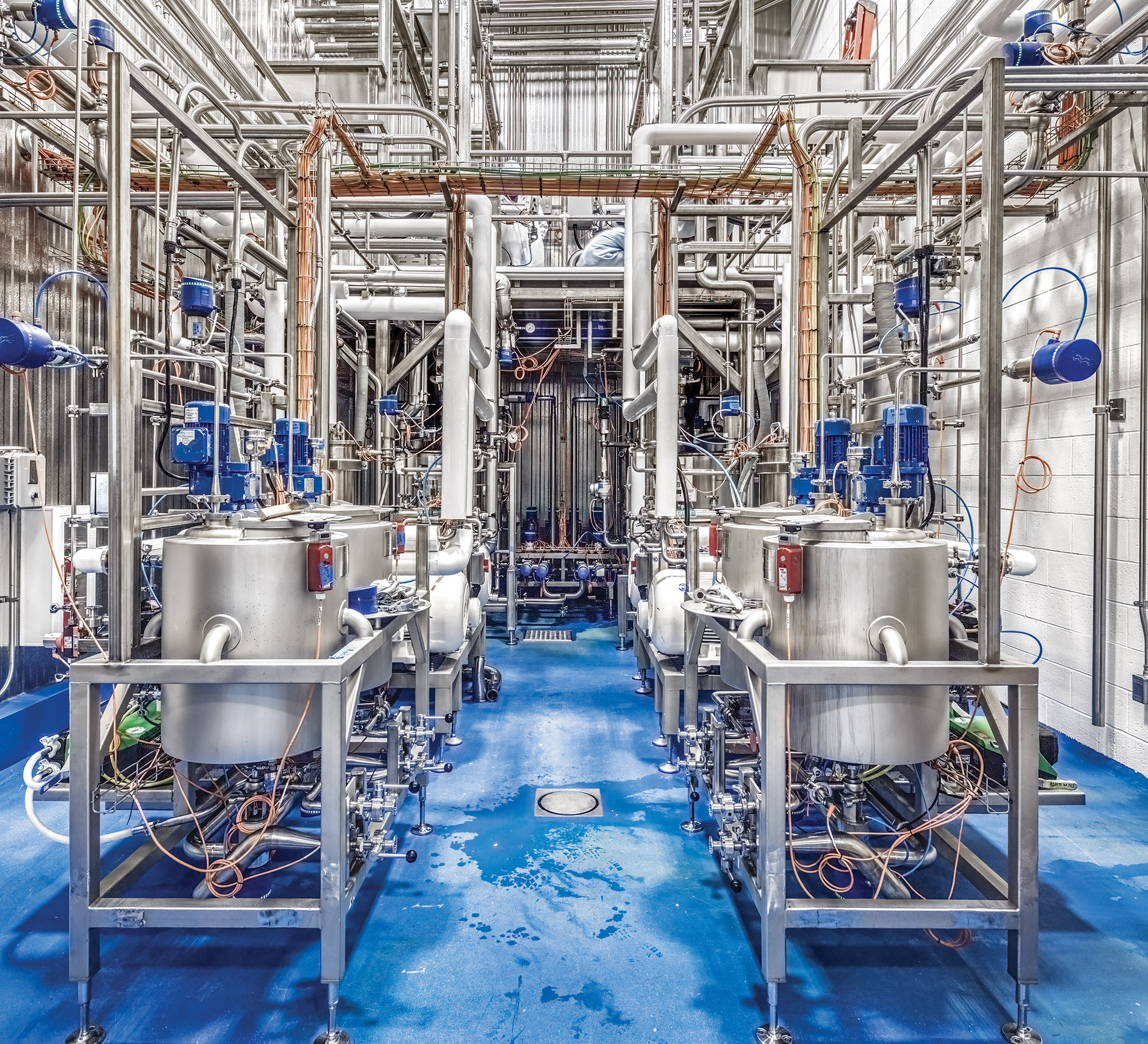
Title
Caption
Title
Caption
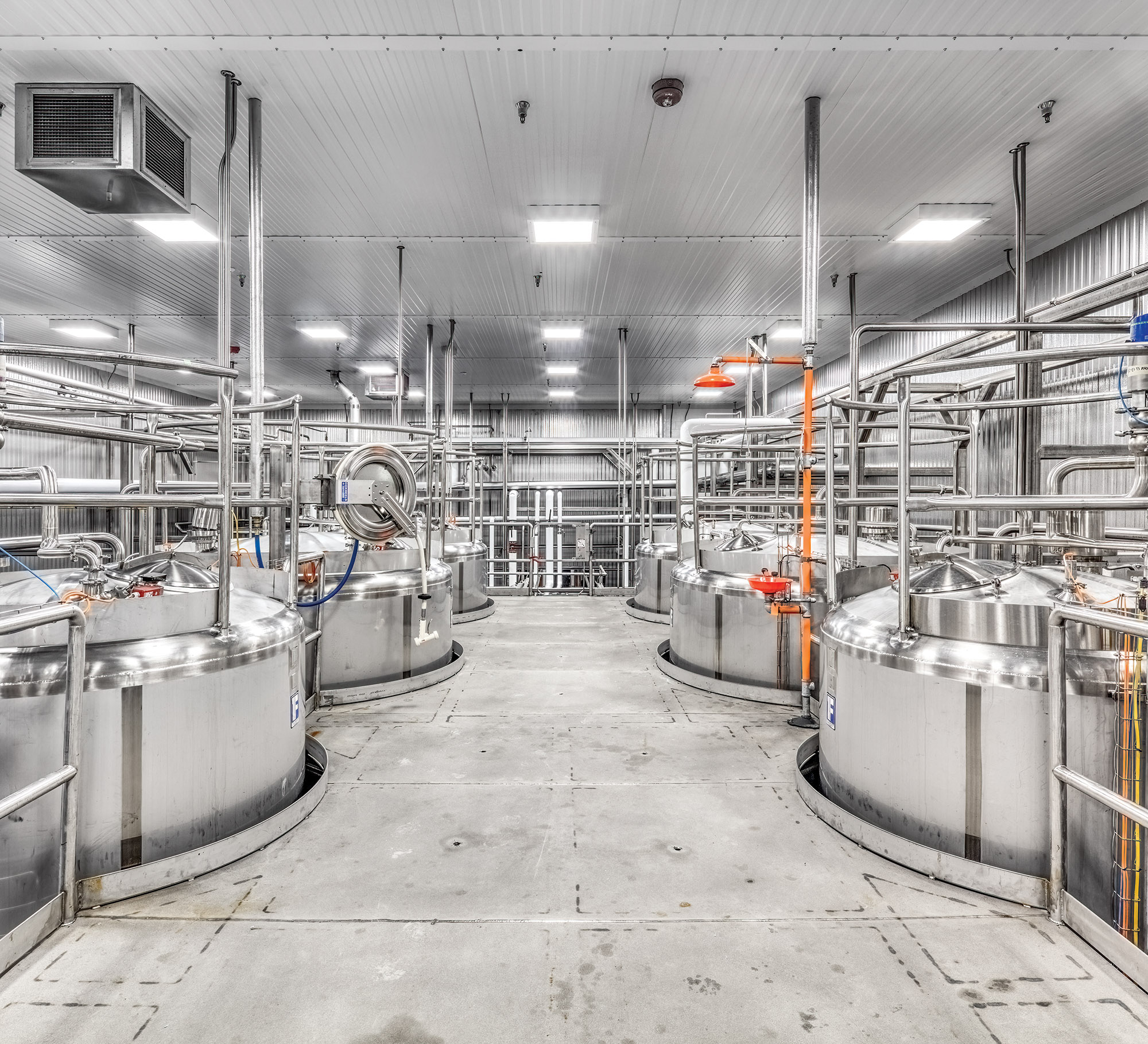
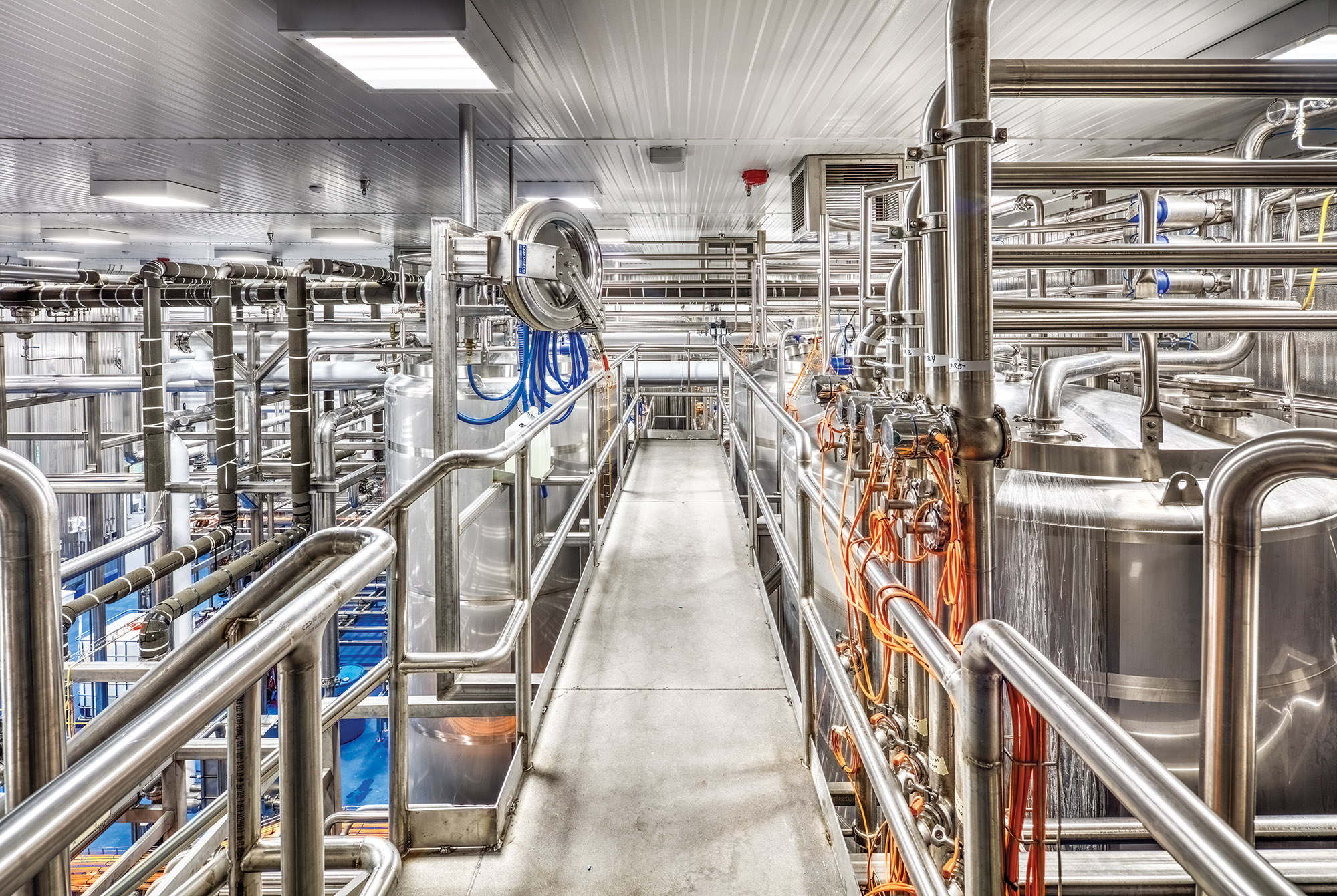
Title
Caption
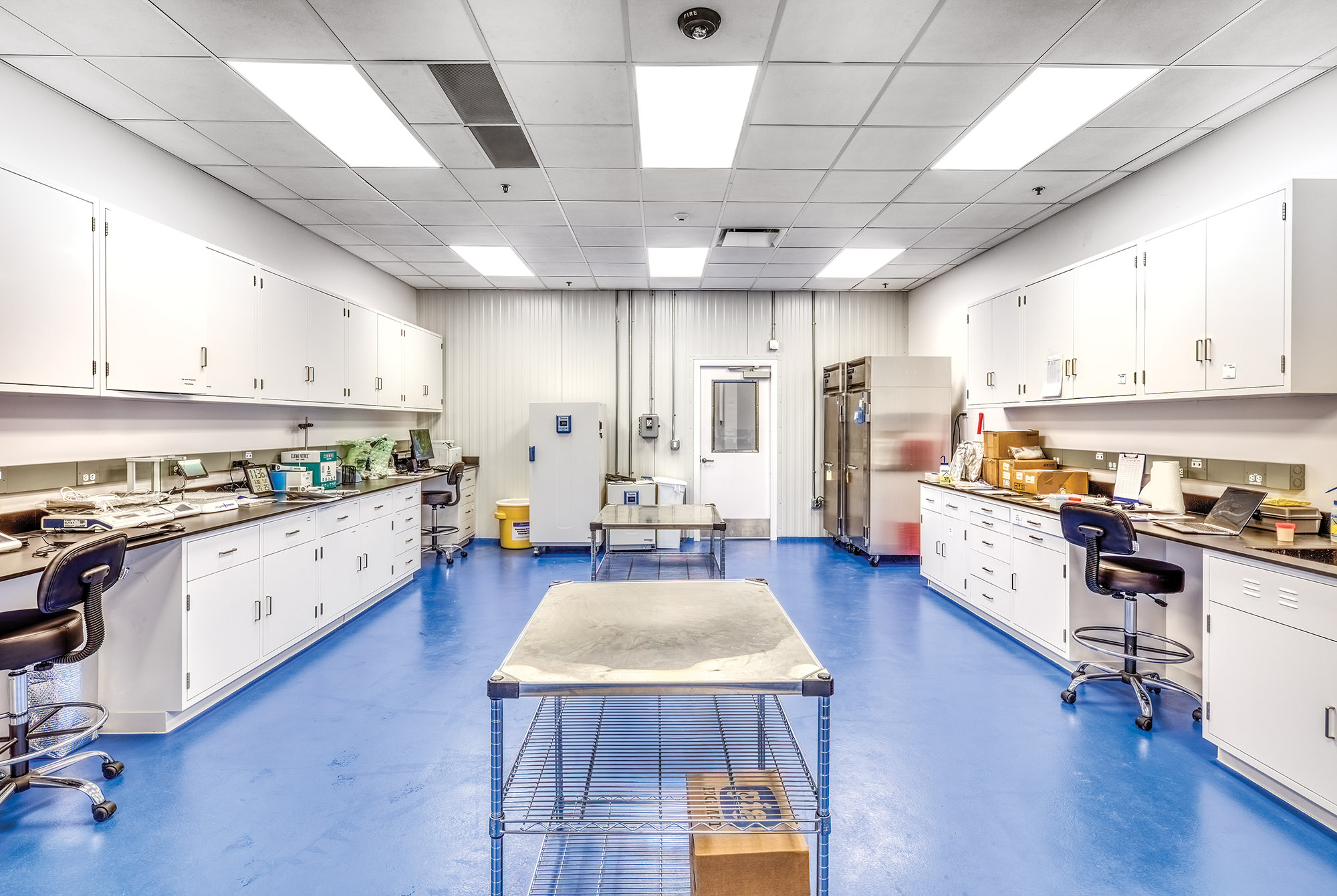
Title
Caption